Depuis 1988 et la reprise de l’entreprise par les descendants du fondateur, Vittorio Pegoraro, Alpego s’agrandit à vue d’œil. Le constructeur emploie 148 salariés en Italie et possède deux usines. La première, installée dans le village historique de Gambellara (Vénétie), confectionne les pièces des outils. En 2014, une seconde unité voit le jour à Lonigo, à quelques kilomètres du cœur historique. Alpego envisage un changement de site à cause de l’impossibilité d’étendre son établissement de Gambellara. L’usine de Lonigo, d’une superficie de 21 000 m2, possède 7 100 m2 couverts. C’est en 2001, alors que l’entreprise ne compte encore que 30 salariés, qu’Alpego ouvre les portes de sa filiale française.
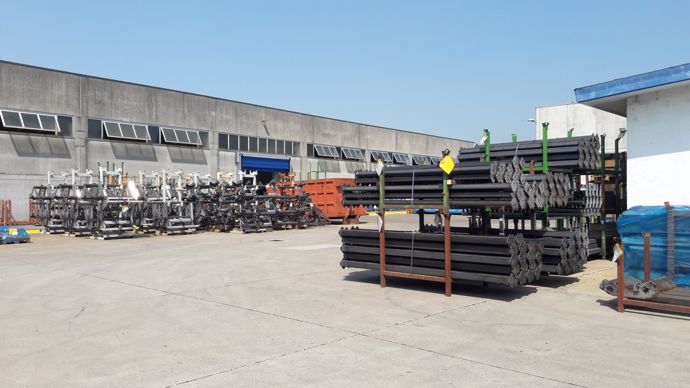
Une production, deux sites
Le siège historique de Gambellara s’occupe désormais de la partie sidérurgie de l’ensemble des outils. Toute la matière première arrive à l’unité. Alpego en consomme 3 500 t par an pour confectionner toutes les gammes d’appareils. L’acier à haute résistance à l’abrasion, fourni par SSAB, est stocké temporairement dans la cour. La première étape consiste à découper toutes les pièces. L’usine possède de multiples outils. Elle se dote d'abord de lasers pour faciliter la découpe des plaques en acier. Selon l’épaisseur de la matière, un opérateur remplace la mine de l’outil, laquelle se change également lorsqu’elle est usée. Alpego utilise ensuite un laser pour l’usinage de ses pièces, garantissant ainsi une qualité similaire entre chaque pièce. Cette technique permet également d’économiser la matière première. Toutes les découpes sont calculées grâce à un logiciel pour minimiser les pertes. Les chutes seront renvoyées chez le fournisseur pour être fondues en nouvelles plaques d’acier. Certaines pièces sont ensuite façonnées par des plieuses. L’entreprise italienne en possède deux. Devant sa grande diversité de pièces, elle n’a aucun avantage à s’équiper de plieuses automatiques. La dernière étape sur le site de Gambellara consiste à assembler certains sous-ensembles. Pour cela, l’usine possède un robot de soudure épaulé par deux soudeurs qui assemblent les endroits inatteignables par l’automate. À l’avenir, l’entreprise aimerait automatiser cet atelier avec l’arrivée de deux autres robots.
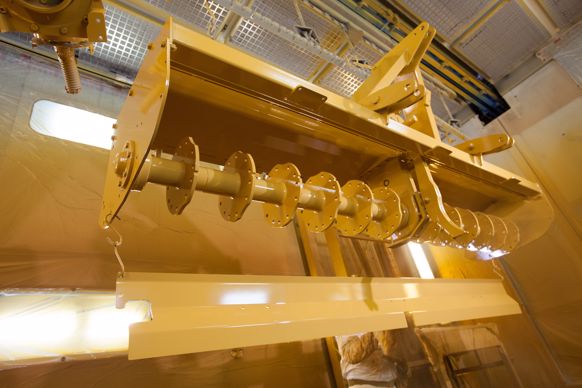
La peinture à Lonigo
Les châssis des outils sont ensuite acheminés sur le site de Lonigo pour être peints puis assemblés avec les dernières pièces. L’étape qui suit l’arrivée des châssis sur place est le montage des différents composants qui recevront le même coloris jaune, à l'instar des boîtiers d’entraînement et des herses rotatives. L’atelier de peinture se divise en trois parties. La première, la partie grenaillage, est commune à toutes les pièces. Ce principe consiste à nettoyer ces dernières et à en éliminer toutes les impuretés. Alpego procède ensuite de deux façons pour recouvrir les outils de leur robe jaune. Pour les pièces possédant un boîtier avec de l’huile, donc sensibles aux hautes températures, une peinture à l’eau, qui sera cuite dans un four entre 80 et 100 °C, est appliquée sur les outils. Pour les autres pièces, telles que les châssis et les tôles de protection, les opérateurs utilisent une peinture en poudre. Cette technique permet une cuisson à une température de 180 °C et assure une meilleure résistance aux chocs. Les machines retournent ensuite sur l’unique chaîne d’assemblage pour les derniers détails, comme les autocollants. En fin de ligne de montage, Alpego effectue un contrôle particulier puisqu’il pèse l’outil pour vérifier qu’il ne manque aucun composant. Cette étape autorise une variation de poids de plus ou moins 300 g, au-delà de laquelle l’outil sera inspecté pour résoudre le problème. Pour son année 2019, Alpego espère produire environ 3 000 machines, dont les deux tiers partiront à l’export.
