Nous avons testé ces remorques avec une ration complète. Onze constructeurs ont répondu à notre invitation, prenant ainsi part au comparatif mené fin avril 2018 sur l'une des exploitations du lycée agricole de Magnac-Laval (Haute-Vienne). Ce travail décrit d'abord le protocole d'étude puis présente les critères prépondérants choisis pour mettre en évidence les principales différences décelées entre les 11 machines étudiées. Ce comparatif concerne les mélangeuses à deux vis verticales d'environ 18 m3 dotées d'une turbine de paillage. La demande pour ce type de machine polyvalente se cantonne principalement au marché français, qui compte néanmoins un grand nombre d'acteurs. Au travers de différentes mises en situation, nous avons évalué le travail de 11 bols pailleurs selon un protocole établi au préalable. L'exploitation agricole choisie pour les essais comptait environ 250 bovins à l'engrais sur la période, logés dans trois bâtiments distincts. Nous avons demandé à chaque constructeur participant de préparer un mélange préalablement défini, composé de 1 500 kg de maïs, 500 kg d'ensilage d'herbe, 500 kg d'aliment concentré et 50 kg de paille.
Retrouvez les 11 bols à l'essai :
BVL Jeantil Kongskilde Kuhn LucasG RMH Robert Silofarmer Strautmann Supertino Trioliet
La ration finale, d'une masse d'environ 2 050 kg, devait comprendre des fibres d'une longueur maximale correspondant à la largeur d'un poing (soit une dizaine de centimètres), selon les recommandations du responsable de l'élevage. L'ordre de chargement et la durée de mélange ont été laissés à la discrétion du constructeur. Afin d'alimenter l'ensemble des bovins en quantités suffisantes, deux rations identiques étaient préparées quotidiennement. Chaque bol permettait ensuite de procéder au paillage d'une série de boxes. Les conseillers en machinisme des chambres d'agriculture de la Haute-Vienne, de la Corrèze, de la Creuse et de la région Nouvelle-Aquitaine, tout comme le personnel de l'exploitation, ont participé aux opérations. Nous tenons ici à les en remercier vivement.
Homogénéité du mélange
Au cours de ce comparatif, nous n'avons pas été en mesure d'évaluer la qualité de mélange des machines testées. Chaque éleveur se fixe l'objectif de disposer d'une ration la plus homogène possible. Les vis de mélange assurent une double fonction : elles brassent et coupent les aliments chargés dans le bol. Pour synthétiser la ration voulue, le constructeur doit donc trouver un bon compromis en brassant amplement les ingrédients, mais sans excès afin de conserver un niveau de fibrosité suffisant, indispensable à la rumination.
Appréciation physique du mélange
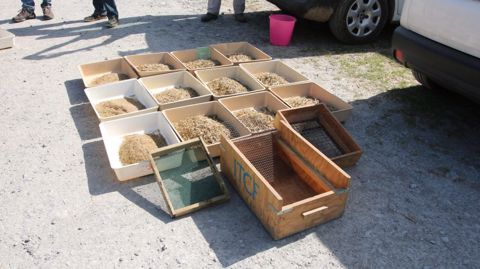
Afin de mettre en évidence l'évolution de la composition physique des ingrédients au cours des phases de mélange et de distribution, nous avons prélevé trois échantillons d'environ 2,5 kg chacun lors de la vidange, lorsque 25, 50 et 75 % de la masse totale du mélange étaient déchargés. Ces prélèvements ont subi un tamisage au travers de mailles de 2, 1 et 0,5 cm, pour chacun des bols pailleurs du comparatif. Les animaux ne ruminant plus lorsque la longueur des brins devient inférieure à 2 cm, nous avons porté exclusivement notre attention sur les quantités de fibres longues (plus de 2 cm) présentes dans le mélange.
Le ratio de la longueur de fibres, établi pour chaque bol, se définit par l'écart entre la proportion moyenne de fibres longues présente dans les ingrédients initiaux et la proportion moyenne des trois prélèvements, ramené à la durée de mélange du bol concerné. Cependant, ce ratio dépend également des réglages de la position des couteaux et des contre-couteaux choisis par chaque opérateur. En comparant le travail produit ce jour-là par les 11 machines, il ressort que le modèle Kuhn présente le ratio de défibrage le plus élevé de notre comparatif (10,7). Les remorques mélangeuses-pailleuses BvL et Trioliet affichent, elles, une capacité de défibrage minimale (1,2).
Fiabilité de la pesée
Une évaluation précise de la quantité chargée en cuve nécessite d'atteler et d'installer la remorque de façon horizontale. Le système de pesée des bols pailleurs de notre comparatif compte entre trois et six capteurs par machine, lesquels mesurent la déformation des bols sous la contrainte. Pour vérifier la précision du système de pesée embarqué sur chaque modèle, nous avons pesé toutes les machines à vide sur la bascule de la coopérative locale. Les évaluations de cet instrument métrologique sont autorisées pour des transactions commerciales et sa marge d'erreur ne dépasse pas 20 kg. À l'issue du chargement des ingrédients de la ration, nous avons à nouveau évalué la masse de chaque machine sur cette bascule. En comparant la différence de ces valeurs à la masse relevée sur le boîtier de pesée de chaque bol, nous avons ainsi pu déduire le niveau de précision fourni par chacun des systèmes de pesée. Il ressort que, sur les modèles évalués, les écarts varient, en valeur absolue, de 0,2 à 3,6 % selon les machines (entre 5 kg pour la mélangeuse Trioliet et 76 kg pour le bol Lucas G).
Quantité de résidus en cuve
Une quantité élevée de résidus en cuve après déchargement complet de la ration peut conduire au vieillissement prématuré des mélangeuses, notamment dans les exploitations distribuant de l'ensilage. Nous avons demandé à chaque constructeur de vidanger le mieux possible son bol pailleur à la fin de la phase de distribution. Pour parvenir à extraire un maximum d'aliments, la plupart de ceux dont les machines étaient entraînées au régime de 540 tr/min ont sélectionné le régime de 1 000 tr/min. À l'issue de cette étape, nous avons récupéré puis pesé le mélange restant dans la cuve de chaque constructeur. Cette masse résiduelle oscille, selon les constructeurs, entre 3,5 kg (Kongskilde) et 48,6 kg (Robert), soit entre 0,2 et 2,3 % de la masse chargée. Il apparaît notamment que la surface et l'inclinaison de l'extrémité supérieure des vis influent sur la quantité de résidus.
Rétention de fragments métalliques
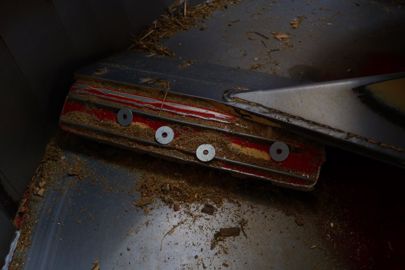
Aujourd'hui, tous les constructeurs installent sur demande un ou plusieurs aimants sur les vis, sur le déflecteur ou sur le tapis en sortie de cuve. Cette option, quoique relativement coûteuse (parfois plus de 1500 € par aimant prix tarif), peut être rentabilisée rapidement lorsqu'elle préserve les bovins d'une réticulo-péritonite causée par l'ingestion de fragments métalliques. L'installation ne fonctionne toutefois qu'avec des fragments de métaux contenant du fer, de cobalt ou de nickel. Les morceaux d'aluminium, par exemple, ne sont donc pas retenus. Pour connaître l'efficacité des aimants à capter de petites pièces métalliques, nous avons incorporé cinq rondelles en acier de 30 mm de diamètre lors du chargement de l'ensilage d'herbe dans le bol. En fin de distribution, nous avons relevé le nombre de rondelles effectivement captées par attraction magnétique. Selon les modèles, cette valeur oscillait entre 0 et 5.
Les bols Lucas G, Strautmann et Trioliet ont réussi un sans-faute sur cette épreuve-là. Les aimants de la remorque mélangeuse Supertino ont en revanche fait chou blanc. Le bol Robert, quant à lui, n'était pas équipé d'aimant. À l'issue de cette expérimentation, il apparaît d'une part que l'emplacement des aimants semble influer sur leur aptitude à capter les fragments métalliques. Implantés le plus souvent à la base des vis, ils présenteraient pour certains une capacité de rétention moindre en raison d'un dégagement insuffisant sous la spire qui les surplombe. D'autre part, la force d'attraction influerait elle aussi sur la capacité de rétention des corps étrangers en métal. Les aimants au néodyme utilisés par une majorité de constructeurs présentent un champ magnétique particulièrement puissant. Ils peuvent endommager tout appareil électrique ou électronique placé à proximité et se révèlent dangereux pour les porteurs de stimulateurs cardiaques.
Paillage
Afin de caractériser les performances du module de paillage, il convient en premier lieu d'évaluer le débit de paillage. Pour déterminer la capacité de chaque turbine, nous avons demandé aux constructeurs de pailler une surface donnée de stabulation après avoir chargé précisément 500 kg de paille dans le bol.
L'intervention de chaque machine a été chronométrée. Il ressort de ce test que le débit de paillage annoncé par certains constructeurs excède parfois largement la capacité réelle de la machine. Pour les 11 bols pailleurs testés, le débit de la turbine oscille ainsi entre 57 et 158 kg/min. La capacité de la turbine à projeter la paille à bonne distance constitue un autre paramètre dans le choix d'un système de paillage. Pour les 11 modèles de ce comparatif, la distance maximale de paillage oscille entre 16 et 28 m. Selon nos mesures, débit et distance maximale de paillage ne semblent être corrélés ni avec le diamètre de la turbine, ni avec la surface de la trappe de paillage. Nous avons en outre évalué le déport de la goulotte de paillage après repliage. Le déport nul voire négatif observé sur certains modèles (Trioliet et Robert, notamment) limite son risque d'arrachement au cours de manœuvres lors de la distribution de la ration.
Puissance absorbée
Avec l'appui de la chambre régionale de Nouvelle-Aquitaine, nous avons évalué la consommation de puissance de chacun des bols pailleurs de ce comparatif, lors des différentes phases de travail.
À l'issue des tests menés sur les bols pailleurs, le tracteur Claas Arion 530 Stage IV utilisé dans ces essais a subi un passage au banc moteur. En modulant la charge, le technicien a ajusté les différents régimes de prise de force utilisés lors des tests et réglé les niveaux de consommation instantanée correspondants. Il en a déduit les puissances consommées pour chaque machine, dans chacune des situations de travail. Les graphiques illustrent les écarts de consommation de puissance déterminés lors de notre comparatif, pour les différentes phases de travail. Selon les machines, les puissances requises oscillent du simple au double : entre 25 et 57 ch pour le mélange (graphique 1). Les tests de distribution (graphique 2) ont exigé entre 27 et 56 ch suivant les constructeurs. Sans surprise, le paillage (graphique 3) est la tâche qui exige le plus de puissance, mais le besoin varie fortement selon la conception des machines, entre 30 et 119 ch absorbés. Le bol pailleur Trioliet, en particulier, s'est montré gourmand en puissance lors de la phase de paillage. En considérant l'ensemble des tâches, la puissance moyenne absorbée par les mélangeuses-pailleuses varie du simple au triple selon les modèles (graphique 4).
Consommation de carburant
Après avoir installé un débitmètre sur le tracteur attelé successivement aux 11 mélangeuses, nous avons relevé à de nombreuses reprises le cumul de consommation lors des différentes étapes de l'expérimentation. Nous avons pu exploiter ces relevés en écartant les valeurs correspondant aux périodes durant lesquelles les ensembles attelés ont manœuvré ou se sont déplacés entre les bâtiments. Seuls les cumuls de consommation correspondant aux séquences durant lesquelles la prise de force tourne importent. Pour la phase de mélange, les besoins en carburant, relativement comparables, oscillent entre 6,6 L/h (Supertino) et 9,7 L/h (Jeantil). Lors de la phase de distribution, ils s'étalent entre 4,7 L/h (Robert) et 19 L/h (Kuhn). La consommation en carburant pour la séquence de paillage oscille, elle, entre 8,3 L/h (Supertino) et 27 L/h (Trioliet) selon les machines. Au final, pour l'ensemble des tâches identiques assurées par chaque machine, la consommation moyenne pondérée par le temps d'intervention varie du simple au double selon le modèle utilisé, entre 6,3 L/h pour Supertino et 12,8 L/h pour Kuhn.
Retrouvez les 11 bols à l'essai :
BVL Jeantil Kongskilde Kuhn LucasG RMH Robert Silofarmer Strautmann Supertino Trioliet